Destylacja rozpuszczalników to proces, który polega na oddzieleniu składników mieszaniny na podstawie różnicy ich temperatur wrzenia. Jest to technika szeroko stosowana w chemii, przemyśle farmaceutycznym oraz w produkcji alkoholi. Proces ten zaczyna się od podgrzewania cieczy, co powoduje jej parowanie. W wyniku tego pary unoszą się do góry i są kierowane do chłodnicy, gdzie skraplają się z powrotem w ciecz. Kluczowym elementem tego procesu jest to, że różne substancje mają różne temperatury wrzenia, co pozwala na ich skuteczne oddzielenie. W przypadku rozpuszczalników, takich jak etanol czy aceton, destylacja może być wykorzystywana do oczyszczania ich z zanieczyszczeń lub do odzyskiwania ich z mieszanin. W praktyce destylacja rozpuszczalników może być przeprowadzana w różnych warunkach, w tym pod ciśnieniem atmosferycznym lub w warunkach próżniowych, co wpływa na efektywność procesu oraz jakość uzyskanego produktu.
Jakie są zastosowania destylacji rozpuszczalników w przemyśle
Destylacja rozpuszczalników znajduje szerokie zastosowanie w różnych branżach przemysłowych, co czyni ją kluczowym procesem technologicznym. W przemyśle chemicznym jest wykorzystywana do oczyszczania surowców oraz produktów końcowych. Na przykład, w produkcji farb i lakierów destylacja pozwala na usunięcie zanieczyszczeń oraz niepożądanych składników, co wpływa na jakość finalnego produktu. W przemyśle farmaceutycznym destylacja jest niezbędna do uzyskiwania czystych substancji czynnych, które są kluczowe dla produkcji leków. Ponadto, w branży spożywczej destylacja służy do produkcji alkoholi oraz ekstraktów smakowych, takich jak olejki eteryczne. Warto również wspomnieć o zastosowaniach destylacji w recyklingu rozpuszczalników organicznych, gdzie proces ten umożliwia odzyskiwanie wartościowych substancji z odpadów przemysłowych.
Jakie są rodzaje destylacji rozpuszczalników i ich różnice
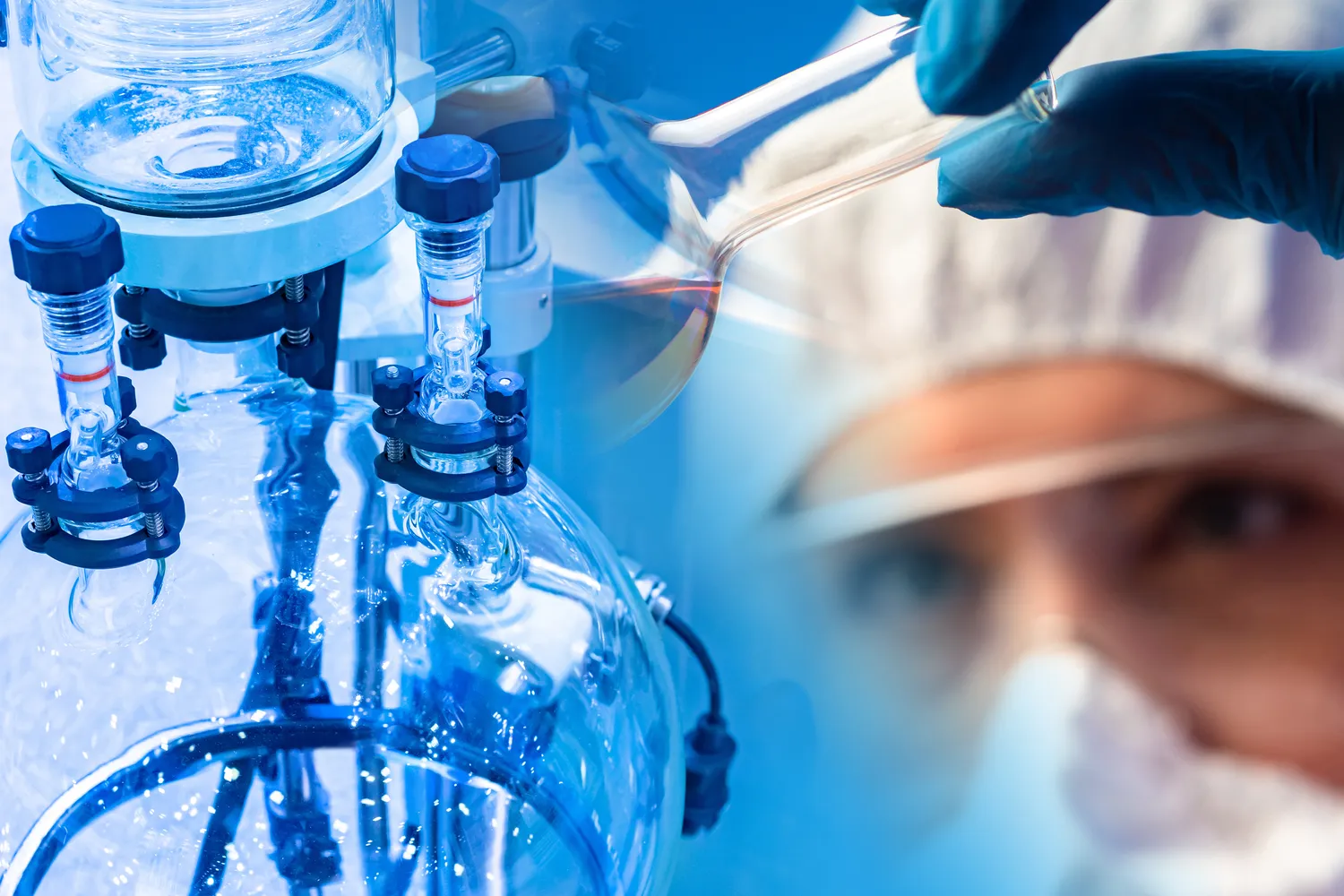
W kontekście destylacji rozpuszczalników wyróżnia się kilka różnych metod, które różnią się między sobą zasadą działania oraz zastosowaniem. Najpopularniejsze rodzaje to destylacja prosta, frakcyjna oraz próżniowa. Destylacja prosta jest najczęściej stosowana do separacji substancji o znacznej różnicy temperatur wrzenia. Proces ten jest stosunkowo łatwy do przeprowadzenia i nie wymaga skomplikowanego sprzętu. Z kolei destylacja frakcyjna jest bardziej zaawansowaną metodą, która pozwala na oddzielanie kilku składników o zbliżonych temperaturach wrzenia. W tym przypadku wykorzystuje się kolumny frakcyjne, które zwiększają efektywność separacji poprzez wielokrotne skraplanie i parowanie substancji. Destylacja próżniowa natomiast odbywa się w obniżonym ciśnieniu, co pozwala na obniżenie temperatury wrzenia substancji i minimalizację ryzyka degradacji termicznej składników.
Jakie są zalety i wady destylacji rozpuszczalników
Destylacja rozpuszczalników ma wiele zalet, które przyczyniają się do jej popularności w różnych dziedzinach przemysłu. Przede wszystkim jest to metoda skuteczna i sprawdzona, która pozwala na uzyskanie wysokiej czystości produktów chemicznych. Ponadto proces ten jest relatywnie prosty do przeprowadzenia i może być dostosowany do różnych skal produkcji – zarówno laboratoryjnej, jak i przemysłowej. Dodatkowo destylacja umożliwia odzyskiwanie cennych substancji z odpadów, co wpływa na efektywność ekonomiczną oraz ochronę środowiska. Niemniej jednak istnieją również pewne wady związane z tą metodą. Proces destylacji może być czasochłonny i wymaga dużej ilości energii, co może zwiększać koszty produkcji. Ponadto niektóre składniki mogą ulegać degradacji podczas podgrzewania, co wpływa na jakość końcowego produktu. Wreszcie skuteczność procesu zależy od właściwości fizykochemicznych separowanych substancji, co może ograniczać jego zastosowanie w niektórych przypadkach.
Jakie są najczęstsze błędy podczas destylacji rozpuszczalników
Podczas przeprowadzania destylacji rozpuszczalników można napotkać wiele pułapek, które mogą prowadzić do nieefektywności procesu oraz obniżenia jakości uzyskiwanego produktu. Jednym z najczęstszych błędów jest niewłaściwe ustawienie temperatury podgrzewania. Zbyt wysoka temperatura może prowadzić do degradacji składników lub ich niepożądanego parowania, co skutkuje zanieczyszczeniem końcowego produktu. Z kolei zbyt niska temperatura może spowodować, że proces destylacji będzie nieefektywny i nie uda się uzyskać oczekiwanego poziomu czystości. Innym powszechnym błędem jest niewłaściwe dobranie sprzętu, takiego jak kolumna frakcyjna czy chłodnica, co może wpływać na efektywność separacji. Ważne jest również, aby dokładnie monitorować proces i kontrolować parametry takie jak ciśnienie czy przepływ chłodziwa, ponieważ ich zmiany mogą znacząco wpłynąć na wyniki destylacji. Oprócz tego, niektóre osoby mogą zaniedbywać przygotowanie surowców przed destylacją, co prowadzi do obecności zanieczyszczeń w mieszaninie.
Jakie są różnice między destylacją a innymi metodami separacji
Destylacja rozpuszczalników to jedna z wielu metod separacji substancji chemicznych, jednak różni się ona od innych technik pod względem zasad działania oraz zastosowań. Na przykład, w przeciwieństwie do filtracji, która polega na oddzieleniu ciał stałych od cieczy przy użyciu porowatych materiałów, destylacja opiera się na różnicy temperatur wrzenia składników. Filtracja jest skuteczna w przypadku mieszanin zawierających cząstki stałe, ale nie sprawdza się w przypadku cieczy o podobnych właściwościach fizykochemicznych. Inną popularną metodą separacji jest ekstrakcja, która polega na wykorzystaniu rozpuszczalników do wydobywania określonych składników z mieszaniny. Ekstrakcja może być bardziej efektywna w przypadku substancji o niskich temperaturach wrzenia lub gdy zachodzi potrzeba selektywnego wydobycia jednego składnika. Warto również wspomnieć o chromatografii, która jest techniką separacyjną opartą na różnicach w przyleganiu składników do fazy stacjonarnej i ruchomej. Chromatografia jest często stosowana w laboratoriach analitycznych do identyfikacji i ilościowego oznaczania substancji chemicznych.
Jakie są nowoczesne technologie związane z destylacją rozpuszczalników
W ostatnich latach rozwój technologii związanych z destylacją rozpuszczalników znacząco wpłynął na efektywność oraz jakość tego procesu. Nowoczesne urządzenia destylacyjne są coraz bardziej zaawansowane i wyposażone w systemy automatyzacji, które pozwalają na precyzyjne kontrolowanie parametrów procesu. Dzięki zastosowaniu inteligentnych czujników możliwe jest monitorowanie temperatury, ciśnienia oraz przepływu w czasie rzeczywistym, co zwiększa bezpieczeństwo oraz efektywność operacji. Ponadto nowoczesne kolumny frakcyjne są projektowane w taki sposób, aby maksymalizować powierzchnię kontaktu między parą a cieczą, co poprawia wydajność separacji. Warto również zwrócić uwagę na rozwój technologii membranowych, które stanowią alternatywę dla tradycyjnej destylacji. Membrany pozwalają na selektywne oddzielanie składników na podstawie ich wielkości lub ładunku elektrycznego, co może być korzystne w przypadku trudnych do oddzielenia substancji. Dodatkowo rośnie zainteresowanie ekologicznymi metodami destylacji, które minimalizują zużycie energii oraz redukują emisję gazów cieplarnianych.
Jakie są wyzwania związane z destylacją rozpuszczalników
Pomimo licznych zalet i zastosowań destylacja rozpuszczalników wiąże się z pewnymi wyzwaniami, które mogą wpływać na jej efektywność i bezpieczeństwo. Jednym z głównych problemów jest konieczność zarządzania dużymi ilościami energii potrzebnej do podgrzewania cieczy oraz chłodzenia par. W obliczu rosnących cen energii oraz globalnych zmian klimatycznych poszukiwanie bardziej energooszczędnych metod staje się kluczowe dla przemysłu chemicznego. Kolejnym wyzwaniem jest ryzyko wystąpienia reakcji chemicznych podczas procesu destylacji, szczególnie gdy przetwarzane są substancje o wysokiej reaktywności lub toksyczności. Dlatego ważne jest stosowanie odpowiednich środków ochrony osobistej oraz przestrzeganie norm bezpieczeństwa podczas pracy z takimi substancjami. Ponadto różnorodność właściwości fizykochemicznych różnych rozpuszczalników sprawia, że dobór odpowiednich parametrów procesu może być skomplikowany i wymaga dużej wiedzy specjalistycznej. Wreszcie problemem mogą być również odpady powstające podczas destylacji, które muszą być odpowiednio zarządzane zgodnie z przepisami ochrony środowiska.
Jakie są przyszłe kierunki badań nad destylacją rozpuszczalników
Przyszłość badań nad destylacją rozpuszczalników zapowiada się obiecująco dzięki rosnącemu zainteresowaniu ekologicznymi i efektywnymi technologiami separacyjnymi. Naukowcy i inżynierowie pracują nad nowymi metodami mającymi na celu zwiększenie wydajności procesów destylacyjnych poprzez zastosowanie zaawansowanych materiałów oraz technologii automatyzacji. Badania koncentrują się również na opracowywaniu nowych rodzajów kolumn frakcyjnych oraz systemów chłodzenia, które mogą znacznie zmniejszyć zużycie energii i poprawić efektywność separacji. Dodatkowo rozwijane są technologie membranowe jako alternatywa dla tradycyjnej destylacji, co może otworzyć nowe możliwości w zakresie separacji trudnych do oddzielenia substancji chemicznych. W kontekście ochrony środowiska badania skupiają się także na minimalizacji odpadów powstających podczas procesu oraz opracowywaniu metod recyklingu rozpuszczalników organicznych. Istotnym kierunkiem badań będzie także analiza wpływu różnych parametrów procesu na jakość uzyskiwanych produktów oraz opracowywanie standardów jakości dla przemysłu chemicznego i farmaceutycznego.