Destylator przemysłowy to zaawansowane urządzenie, które odgrywa kluczową rolę w procesach separacji i oczyszczania różnych substancji chemicznych. Jego głównym zadaniem jest oddzielanie składników mieszanin na podstawie różnic w temperaturze wrzenia. W przemyśle chemicznym, petrochemicznym oraz spożywczym, destylatory są wykorzystywane do produkcji wysokiej jakości produktów, takich jak alkohole, oleje czy różne chemikalia. Kluczowymi cechami destylatora przemysłowego są jego wydajność, zdolność do pracy w wysokich temperaturach oraz odporność na korozję. Wydajność destylatora zależy od jego konstrukcji oraz zastosowanych materiałów. Wysokiej jakości materiały, takie jak stal nierdzewna czy szkło borokrzemowe, zapewniają długotrwałość i efektywność działania. Dodatkowo, nowoczesne destylatory są często wyposażone w systemy automatyzacji, które umożliwiają precyzyjne kontrolowanie parametrów procesu, co zwiększa ich efektywność i bezpieczeństwo użytkowania.
Jakie zastosowania mają destylatory przemysłowe w przemyśle
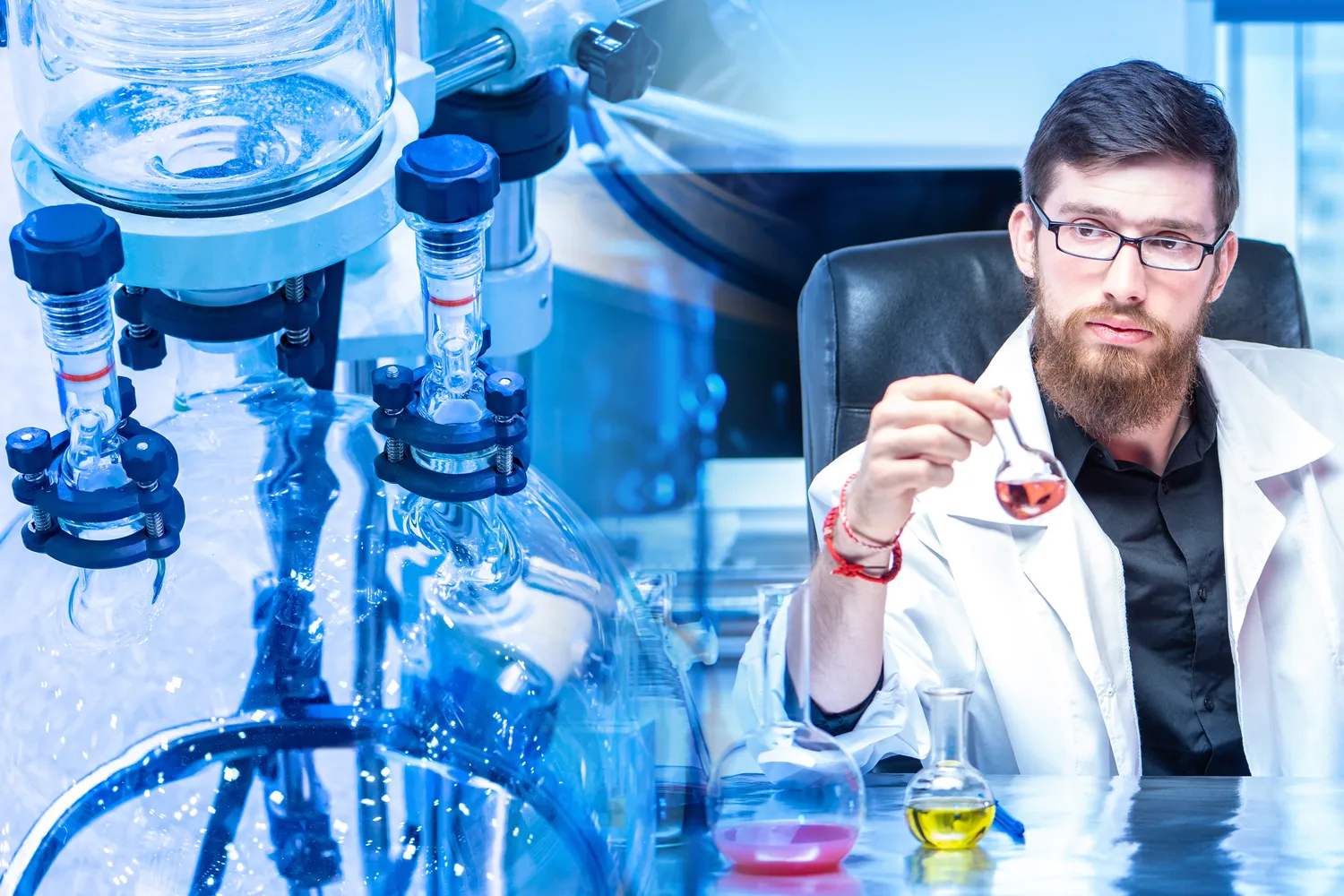
Destylatory przemysłowe znajdują szerokie zastosowanie w różnych branżach, co czyni je niezbędnym elementem wielu procesów produkcyjnych. W przemyśle chemicznym są wykorzystywane do separacji składników reakcji chemicznych oraz oczyszczania produktów końcowych. Na przykład, w produkcji alkoholi etylowych destylatory pozwalają na uzyskanie wysokiej czystości trunków poprzez usunięcie niepożądanych substancji. W branży petrochemicznej destylatory służą do rozdzielania frakcji ropy naftowej, co jest kluczowe dla produkcji paliw oraz innych produktów naftowych. Ponadto w przemyśle farmaceutycznym destylacja jest stosowana do oczyszczania substancji czynnych oraz rozpuszczalników. Dzięki swojej wszechstronności, destylatory przemysłowe mogą być również używane w laboratoriach badawczych do przeprowadzania eksperymentów związanych z separacją substancji chemicznych.
Jakie są różnice między różnymi typami destylatorów przemysłowych
Wybór odpowiedniego typu destylatora przemysłowego ma kluczowe znaczenie dla efektywności procesu produkcyjnego. Istnieje wiele rodzajów destylatorów, a ich różnice wynikają przede wszystkim z zastosowanej technologii oraz przeznaczenia. Destylatory prostoliniowe są najprostsze i najczęściej stosowane w małych instalacjach, gdzie procesy nie wymagają dużej precyzji. Z kolei destylatory frakcyjne charakteryzują się bardziej skomplikowaną budową i pozwalają na separację wielu składników jednocześnie dzięki zastosowaniu kolumny frakcyjnej. Tego typu urządzenia są szczególnie przydatne w przemyśle petrochemicznym i chemicznym. Innym przykładem są destylatory próżniowe, które działają w obniżonym ciśnieniu, co pozwala na destylację substancji o wysokich temperaturach wrzenia bez ryzyka ich rozkładu.
Jakie innowacje technologiczne wpływają na rozwój destylatorów przemysłowych
Innowacje technologiczne mają ogromny wpływ na rozwój i efektywność destylatorów przemysłowych. W ostatnich latach obserwuje się znaczący postęp w zakresie automatyzacji procesów oraz zastosowania nowoczesnych materiałów konstrukcyjnych. Systemy automatyzacji umożliwiają precyzyjne monitorowanie i kontrolowanie parametrów pracy urządzeń, co przekłada się na wyższą jakość produktów oraz oszczędności energetyczne. Dodatkowo nowoczesne technologie pozwalają na optymalizację procesów destylacyjnych poprzez zastosowanie inteligentnych algorytmów sterujących, które analizują dane w czasie rzeczywistym i dostosowują parametry pracy urządzenia do zmieniających się warunków. Kolejnym istotnym trendem jest rozwój ekologicznych technologii destylacji, takich jak wykorzystanie energii słonecznej czy geotermalnej do zasilania procesów produkcyjnych. Dzięki tym innowacjom możliwe jest zmniejszenie zużycia energii oraz emisji szkodliwych substancji do atmosfery.
Jakie są kluczowe aspekty bezpieczeństwa w użytkowaniu destylatorów przemysłowych
Bezpieczeństwo użytkowania destylatorów przemysłowych jest niezwykle istotnym zagadnieniem, które wymaga szczególnej uwagi ze strony producentów oraz operatorów tych urządzeń. Proces destylacji wiąże się z wysokimi temperaturami oraz ciśnieniami, co stwarza ryzyko wystąpienia awarii lub wypadków. Kluczowym aspektem bezpieczeństwa jest odpowiednie zaprojektowanie systemu wentylacji oraz odprowadzania par, aby zminimalizować ryzyko wybuchu lub pożaru. Warto również zwrócić uwagę na materiały użyte do budowy destylatora, które powinny być odporne na korozję oraz wysokie temperatury. Regularne przeglądy techniczne i konserwacja urządzeń są niezbędne do zapewnienia ich prawidłowego funkcjonowania oraz wykrywania potencjalnych usterek. Operatorzy powinni być odpowiednio przeszkoleni w zakresie obsługi destylatorów oraz znajomości procedur awaryjnych, co pozwoli na szybką reakcję w przypadku wystąpienia nieprzewidzianych sytuacji.
Jakie są koszty zakupu i eksploatacji destylatorów przemysłowych
Koszty zakupu i eksploatacji destylatorów przemysłowych mogą znacznie się różnić w zależności od ich typu, wielkości oraz zastosowanej technologii. Inwestycja w nowoczesny destylator często wiąże się z wysokimi kosztami początkowymi, jednak warto pamiętać, że długoterminowe oszczędności wynikające z efektywności energetycznej oraz automatyzacji procesów mogą zrekompensować te wydatki. Koszty eksploatacji obejmują przede wszystkim zużycie energii, konserwację oraz ewentualne naprawy. W przypadku destylatorów o dużej wydajności, koszty operacyjne mogą być znacznie niższe dzięki optymalizacji procesów i zastosowaniu nowoczesnych rozwiązań technologicznych. Dodatkowo warto uwzględnić koszty związane z zatrudnieniem wykwalifikowanego personelu do obsługi urządzeń oraz przeprowadzania regularnych przeglądów technicznych. Wybór odpowiedniego dostawcy sprzętu oraz materiałów eksploatacyjnych również ma wpływ na całkowite koszty użytkowania destylatora.
Jakie są najczęstsze problemy związane z działaniem destylatorów przemysłowych
Destylatory przemysłowe, mimo swojej zaawansowanej technologii, mogą napotykać różnorodne problemy podczas eksploatacji. Jednym z najczęstszych problemów jest osadzanie się zanieczyszczeń wewnątrz urządzenia, co może prowadzić do obniżenia efektywności procesu destylacji. Zanieczyszczenia te mogą pochodzić zarówno z surowców, jak i z samego procesu produkcji. Regularne czyszczenie i konserwacja są kluczowe dla utrzymania optymalnej wydajności destylatora. Innym problemem mogą być nieprawidłowe ustawienia parametrów pracy urządzenia, co może prowadzić do niewłaściwej separacji składników i obniżenia jakości produktu końcowego. W takich przypadkach konieczne jest przeprowadzenie analizy procesów oraz dostosowanie ustawień zgodnie z wymaganiami technologicznymi. Awaria elementów mechanicznych lub elektronicznych również stanowi istotne wyzwanie dla operatorów destylatorów.
Jakie są przyszłościowe kierunki rozwoju technologii destylacji przemysłowej
Przemysłowa technologia destylacji znajduje się w ciągłym rozwoju, a przyszłościowe kierunki tego rozwoju koncentrują się na zwiększeniu efektywności energetycznej oraz minimalizacji wpływu na środowisko. Coraz większą popularnością cieszą się technologie wykorzystujące energię odnawialną do wspomagania procesów destylacyjnych, co pozwala na redukcję emisji CO2 oraz obniżenie kosztów operacyjnych. Również rozwój nanotechnologii otwiera nowe możliwości w zakresie konstrukcji materiałów wykorzystywanych do budowy kolumn destylacyjnych, co może przyczynić się do poprawy efektywności separacji składników. Zastosowanie sztucznej inteligencji i uczenia maszynowego w monitorowaniu procesów produkcyjnych pozwala na bardziej precyzyjne prognozowanie potrzeb związanych z surowcami oraz optymalizację parametrów pracy urządzeń w czasie rzeczywistym. Warto również zwrócić uwagę na rosnącą tendencję do integracji różnych procesów chemicznych i technologicznych w jedną spójną linię produkcyjną, co zwiększa efektywność całego procesu produkcyjnego.
Jakie są różnice między małymi a dużymi destylatorami przemysłowymi
Różnice między małymi a dużymi destylatorami przemysłowymi dotyczą nie tylko ich rozmiarów, ale także zastosowania oraz efektywności operacyjnej. Małe destylatory często znajdują zastosowanie w laboratoriach badawczych lub małych przedsiębiorstwach produkujących specjalistyczne produkty, takie jak alkohole rzemieślnicze czy ekstrakty roślinne. Ich konstrukcja jest zazwyczaj prostsza, co ułatwia obsługę i konserwację, a także zmniejsza koszty początkowe inwestycji. Z kolei duże destylatory przemysłowe są projektowane z myślą o masowej produkcji i charakteryzują się bardziej skomplikowaną budową oraz zaawansowanymi systemami automatyzacji. Dzięki swojej wydajności potrafią przetwarzać znacznie większe ilości surowców w krótszym czasie, co przekłada się na niższe koszty jednostkowe produkcji. Duże instalacje często wymagają również bardziej skomplikowanych systemów zarządzania procesem produkcyjnym oraz wykwalifikowanego personelu do ich obsługi.
Jakie są najważniejsze trendy w branży destylacji przemysłowej
Branża destylacji przemysłowej przechodzi dynamiczne zmiany pod wpływem rosnących wymagań dotyczących efektywności energetycznej i ochrony środowiska. Jednym z najważniejszych trendów jest dążenie do minimalizacji zużycia energii poprzez zastosowanie nowoczesnych technologii i materiałów konstrukcyjnych, które pozwalają na optymalizację procesów produkcyjnych. Coraz częściej przedsiębiorstwa decydują się na inwestycje w systemy odzysku ciepła czy technologie wspomagające wykorzystanie energii odnawialnej. Kolejnym istotnym trendem jest automatyzacja procesów produkcyjnych, która pozwala na zwiększenie wydajności oraz poprawę jakości produktów końcowych poprzez precyzyjne sterowanie parametrami pracy urządzeń. Również rozwój cyfryzacji i Internetu rzeczy (IoT) staje się coraz bardziej widoczny w branży destylacyjnej, umożliwiając zbieranie danych i analizę procesów w czasie rzeczywistym.