Przemysł to jeden z kluczowych sektorów gospodarki, który zajmuje się wytwarzaniem dóbr materialnych poprzez przetwarzanie surowców. W szerokim ujęciu przemysł obejmuje różnorodne dziedziny, takie jak przemysł ciężki, lekki, chemiczny, elektroniczny czy spożywczy. Jego znaczenie w gospodarce jest nie do przecenienia, ponieważ to właśnie przemysł generuje miejsca pracy, przyczynia się do wzrostu PKB oraz wpływa na innowacyjność i rozwój technologiczny. W miarę jak społeczeństwa się rozwijają, potrzeby konsumentów rosną, co prowadzi do zwiększonego zapotrzebowania na różnorodne produkty. Przemysł staje się więc nie tylko źródłem dochodów dla wielu osób, ale również fundamentem dla rozwoju infrastruktury i usług. Warto zwrócić uwagę na to, że przemysł nie działa w izolacji; jego rozwój jest ściśle związany z innymi sektorami gospodarki, takimi jak rolnictwo czy usługi.
Jakie są główne rodzaje przemysłu i ich charakterystyka
Przemysł można podzielić na wiele kategorii, z których każda ma swoje unikalne cechy oraz wymagania. Przemysł ciężki koncentruje się na wydobyciu surowców oraz ich przetwarzaniu na dużą skalę. W tym przypadku mowa o branżach takich jak górnictwo czy hutnictwo. Z kolei przemysł lekki obejmuje produkcję dóbr konsumpcyjnych, takich jak odzież czy elektronika użytkowa. Warto również wspomnieć o przemyśle chemicznym, który zajmuje się produkcją substancji chemicznych wykorzystywanych w różnych dziedzinach życia codziennego oraz przemysłu. Przemysł spożywczy natomiast odpowiada za przetwarzanie surowców rolnych na gotowe produkty żywnościowe. Każdy z tych rodzajów przemysłu ma swoje specyficzne wymagania dotyczące technologii, surowców oraz siły roboczej.
Jakie są wyzwania stojące przed przemysłem w XXI wieku
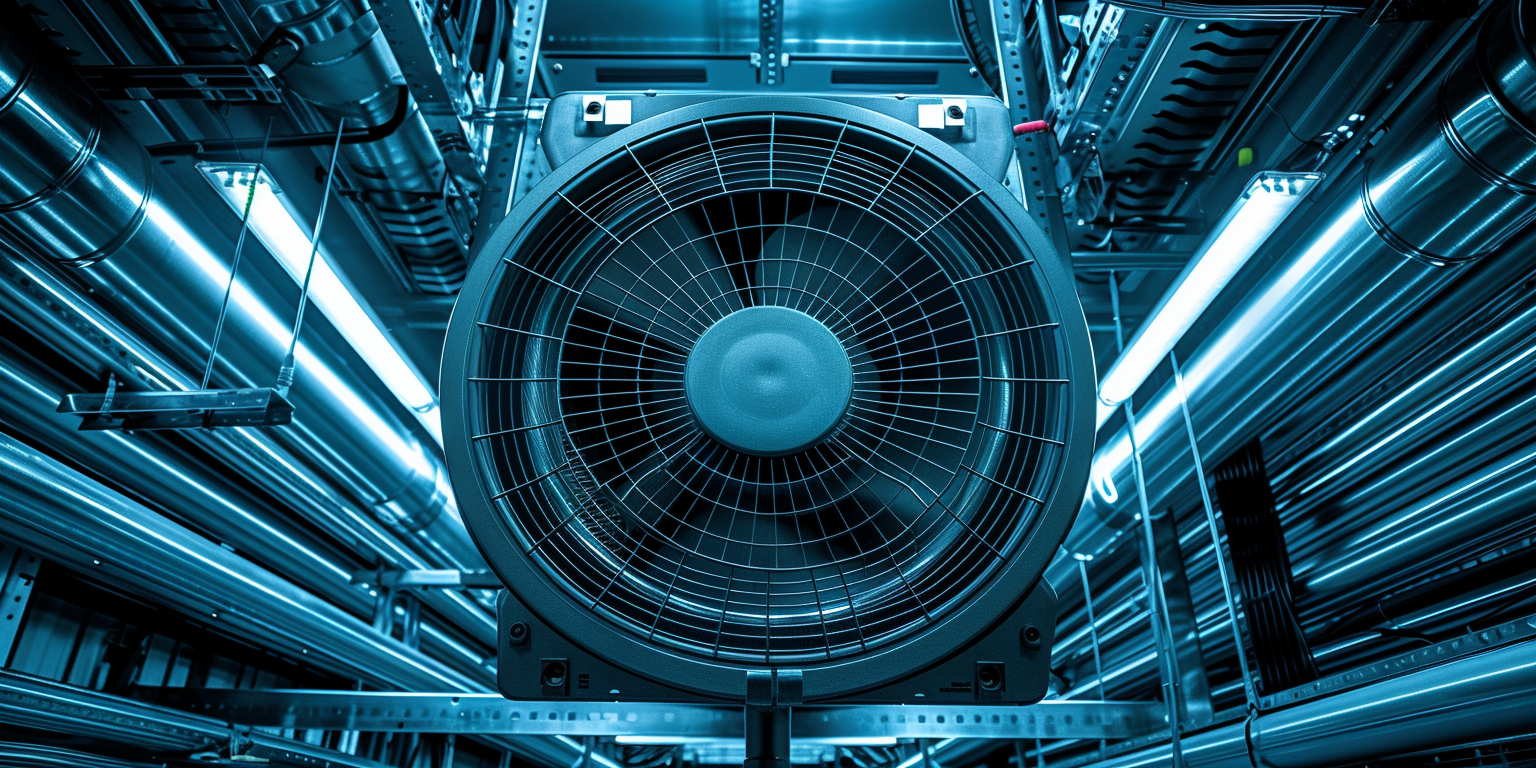
Współczesny przemysł stoi przed wieloma wyzwaniami, które mają wpływ na jego rozwój oraz przyszłość. Jednym z najważniejszych problemów jest konieczność dostosowania się do zmieniających się norm ekologicznych oraz społecznych. W obliczu globalnych zmian klimatycznych przedsiębiorstwa muszą inwestować w technologie przyjazne dla środowiska oraz wdrażać praktyki zrównoważonego rozwoju. Kolejnym wyzwaniem jest automatyzacja i cyfryzacja procesów produkcyjnych. Wprowadzenie nowoczesnych technologii, takich jak sztuczna inteligencja czy Internet Rzeczy, może znacznie zwiększyć efektywność produkcji, ale jednocześnie rodzi obawy o utratę miejsc pracy. Przemysł musi również radzić sobie z globalną konkurencją i zmieniającymi się preferencjami konsumentów.
Jakie są kluczowe trendy w rozwoju przemysłu
W ostatnich latach można zaobserwować kilka kluczowych trendów wpływających na rozwój przemysłu. Jednym z nich jest rosnąca automatyzacja procesów produkcyjnych, która pozwala na zwiększenie wydajności oraz redukcję kosztów operacyjnych. Wprowadzenie robotyzacji i sztucznej inteligencji staje się standardem w wielu branżach, co umożliwia szybsze i bardziej precyzyjne wykonywanie zadań. Kolejnym istotnym trendem jest digitalizacja, która zmienia sposób zarządzania produkcją oraz komunikacji między różnymi działami przedsiębiorstw. Dzięki nowoczesnym technologiom możliwe jest zbieranie danych w czasie rzeczywistym oraz ich analiza, co pozwala na lepsze podejmowanie decyzji biznesowych. Zrównoważony rozwój staje się również priorytetem dla wielu firm; coraz więcej przedsiębiorstw stara się minimalizować swój wpływ na środowisko poprzez wdrażanie ekologicznych praktyk produkcyjnych oraz korzystanie z odnawialnych źródeł energii.
Jakie są kluczowe technologie wpływające na przemysł
W dzisiejszym przemyśle kluczową rolę odgrywają nowoczesne technologie, które rewolucjonizują procesy produkcyjne oraz zarządzanie. Jedną z najważniejszych technologii jest Internet Rzeczy (IoT), który pozwala na połączenie różnych urządzeń i maszyn w sieć, umożliwiając ich zdalne monitorowanie i zarządzanie. Dzięki IoT przedsiębiorstwa mogą zbierać dane o wydajności maszyn, co pozwala na optymalizację procesów oraz szybsze identyfikowanie problemów. Kolejną istotną technologią jest sztuczna inteligencja, która znajduje zastosowanie w analizie danych oraz automatyzacji procesów decyzyjnych. AI może przewidywać awarie maszyn, co pozwala na planowanie konserwacji i minimalizację przestojów. Warto również wspomnieć o technologii druku 3D, która rewolucjonizuje sposób produkcji, umożliwiając tworzenie skomplikowanych struktur z różnych materiałów w krótkim czasie.
Jak przemysł wpływa na lokalne społeczności i rozwój regionalny
Przemysł ma znaczący wpływ na lokalne społeczności oraz rozwój regionalny. Przede wszystkim generuje miejsca pracy, co przyczynia się do wzrostu dochodów mieszkańców oraz poprawy ich jakości życia. W regionach, gdzie przemysł jest silnie rozwinięty, często obserwuje się wzrost inwestycji w infrastrukturę, taką jak drogi, szkoły czy szpitale. Przemysł także stymuluje rozwój sektora usługowego, ponieważ rosnące zapotrzebowanie na usługi transportowe, logistyczne czy doradcze sprzyja powstawaniu nowych firm i miejsc pracy. Jednakże wpływ przemysłu na lokalne społeczności nie zawsze jest pozytywny; mogą występować negatywne skutki związane z zanieczyszczeniem środowiska czy degradacją terenów naturalnych. Dlatego ważne jest, aby rozwój przemysłu odbywał się w sposób zrównoważony i odpowiedzialny społecznie.
Jakie są perspektywy rozwoju przemysłu w przyszłości
Perspektywy rozwoju przemysłu w przyszłości są obiecujące, jednak wiążą się z wieloma wyzwaniami i zmianami. W miarę jak technologia będzie się rozwijać, przemysł będzie musiał dostosować się do nowych realiów rynkowych oraz oczekiwań konsumentów. Wzrost znaczenia zrównoważonego rozwoju sprawi, że firmy będą musiały inwestować w ekologiczne technologie oraz praktyki produkcyjne. Można spodziewać się dalszego wzrostu automatyzacji i cyfryzacji procesów produkcyjnych, co wpłynie na struktury zatrudnienia i wymagania dotyczące umiejętności pracowników. Przemysł 4.0 stanie się standardem w wielu branżach, a przedsiębiorstwa będą musiały być elastyczne i gotowe do szybkiego reagowania na zmiany rynkowe. Warto również zauważyć rosnącą rolę innowacji oraz badań i rozwoju; firmy inwestujące w nowe technologie będą miały przewagę konkurencyjną na rynku.
Jakie są korzyści płynące z innowacji w przemyśle
Innowacje w przemyśle przynoszą wiele korzyści zarówno dla przedsiębiorstw, jak i dla społeczeństwa jako całości. Przede wszystkim innowacyjne rozwiązania technologiczne pozwalają na zwiększenie efektywności produkcji oraz redukcję kosztów operacyjnych. Dzięki nowym metodom produkcji możliwe jest osiągnięcie wyższej jakości produktów przy jednoczesnym zmniejszeniu zużycia surowców i energii. Innowacje mogą także prowadzić do powstawania nowych produktów i usług, które odpowiadają na zmieniające się potrzeby konsumentów. Wprowadzenie nowoczesnych technologii może przyczynić się do poprawy warunków pracy oraz bezpieczeństwa pracowników poprzez automatyzację niebezpiecznych procesów czy zastosowanie inteligentnych systemów monitorowania. Dodatkowo innowacje mogą wspierać zrównoważony rozwój poprzez wdrażanie ekologicznych rozwiązań produkcyjnych oraz ograniczenie negatywnego wpływu na środowisko naturalne.
Jakie są różnice między przemysłem a innymi sektorami gospodarki
Przemysł różni się od innych sektorów gospodarki pod względem charakterystyki działalności oraz sposobu generowania wartości dodanej. Główna różnica polega na tym, że przemysł zajmuje się wytwarzaniem dóbr materialnych poprzez przetwarzanie surowców, podczas gdy sektor usług koncentruje się na świadczeniu usług niematerialnych dla klientów. Sektor rolnictwa natomiast zajmuje się uprawą roślin i hodowlą zwierząt, co stanowi podstawę dla przemysłu spożywczego. Przemysł często wymaga dużych nakładów inwestycyjnych w maszyny i technologie, podczas gdy sektor usług może być bardziej elastyczny pod względem kosztów początkowych. Ponadto przemysł charakteryzuje się większą zależnością od surowców naturalnych oraz energii niż inne sektory gospodarki. Zmiany w cenach surowców mogą mieć istotny wpływ na rentowność przedsiębiorstw przemysłowych, podczas gdy sektor usług może być mniej podatny na takie fluktuacje.
Jakie są zasady efektywnego zarządzania w przemyśle
Efektywne zarządzanie w przemyśle opiera się na kilku kluczowych zasadach, które pozwalają osiągnąć wysoką wydajność oraz jakość produkcji. Przede wszystkim ważne jest planowanie i organizacja procesów produkcyjnych; dobrze opracowany harmonogram pracy pozwala uniknąć przestojów oraz zwiększyć efektywność wykorzystania zasobów. Kolejnym istotnym elementem jest monitorowanie wyników produkcji; regularna analiza danych pozwala identyfikować obszary wymagające poprawy oraz podejmować odpowiednie działania korygujące. Współpraca zespołowa jest również kluczowa; zaangażowanie pracowników w procesy decyzyjne sprzyja lepszemu wykorzystaniu ich wiedzy i umiejętności oraz zwiększa motywację do pracy. Ważnym aspektem efektywnego zarządzania jest również dbałość o jakość produktów; wdrażanie systemów zarządzania jakością pozwala minimalizować błędy produkcyjne oraz zwiększać satysfakcję klientów.
Jakie są przykłady udanych transformacji przemysłowych
W historii można znaleźć wiele przykładów udanych transformacji przemysłowych, które przyczyniły się do znacznego wzrostu efektywności oraz innowacyjności firm. Jednym z najbardziej znanych przypadków jest transformacja sektora motoryzacyjnego w Stanach Zjednoczonych podczas lat 80-tych XX wieku, kiedy to firmy takie jak Ford czy General Motors zaczęły wdrażać zasady lean manufacturing, co pozwoliło im znacznie obniżyć koszty produkcji i poprawić jakość pojazdów.